Transformers are some of the most critical equipment in a grid or substation. Consequently, maintaining these tools is crucial, but conventional monitoring techniques are time-consuming, disruptive and limited. Online monitoring solutions offer a better way forward.
Online monitoring is nothing new, though past technologies could only measure a limited range of factors. Today’s Internet of Things (IoT) sensors can provide remote readings of virtually every maintenance indicator, making online monitoring far more helpful. Here are seven of the most significant benefits of using these systems.
Preventing Emergencies
One of the most critical advantages of online transformer monitoring is preventing outages and similar emergencies. IoT devices can warn employees of incoming maintenance issues in real-time, enabling faster responses. Workers can then address these problems before they cause significant disruption and help prevent a disaster.
Recent large-scale outages highlight how critical these early responses can be. Power grid failures in Texas in 2021 led to 246 deaths related to freezing temperatures as millions of residents lost power for extended periods. Resolving issues earlier can ensure wide-scale disruption like this doesn’t happen, potentially saving lives.
In a less dramatic scenario, preventing breakages will help energy companies avoid replacing expensive equipment. It’ll also likely take less time to resolve the issue. Disaster prevention hinges almost entirely on early responses — and that requires real-time warnings, which only online monitoring tools provide.
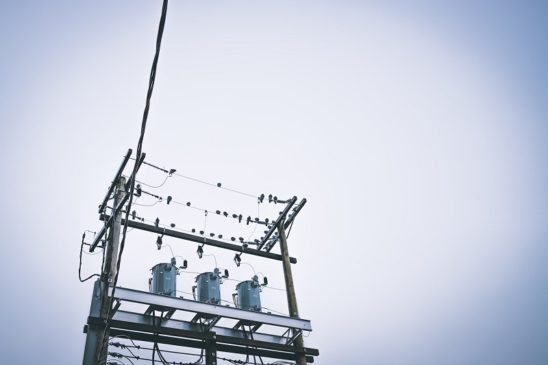
Minimizing Downtime
Relatedly, using online monitoring systems can minimize transformer downtime. Some teams can arrive on-site within 24 hours to respond to maintenance concerns and online warnings mobilize them as early as possible. As a result, power companies can perform repairs faster, reducing any necessary downtime before the transformer is back at peak performance.
Online monitoring solutions further reduce downtime by providing a more streamlined solution to maintenance checks. Many offline monitoring techniques involve shutting machinery off to take and analyze samples. Consequently, routine maintenance can create considerable downtime over a year. IoT sensors can provide these readings without turning the equipment off, maximizing uptime.
Fixing issues before they cause more extensive disruptions will also take less time than resolving a complete outage. Compared to offline solutions, online monitoring reduces downtime in virtually every process.
Higher Employee Productivity
The accessibility and efficiency of these online systems also impact productivity within the workforce. Workers don’t have to travel to and interact with transformers to monitor them with an online system. They can simply pull up readings on a computer or even on their phones, giving them more time to focus on other tasks.
While transformer monitoring is critical, manual approaches consume more time than necessary. Most of the time employees spend on them isn’t impactful work, consisting primarily of walking. Online systems remove travel and physical interactions from the process, streamlining it to its most essential parts. As a result, employees can perform this work without taking much time from other pressing matters.
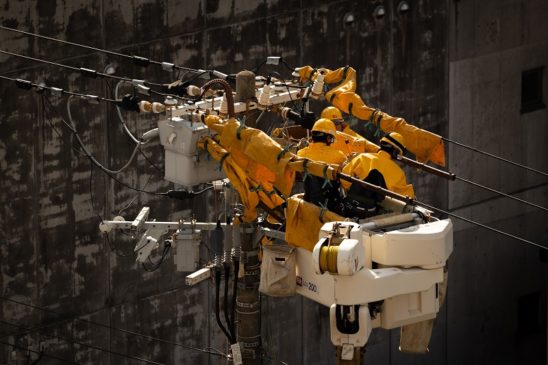
Reduced Maintenance Costs
Using online systems to monitor power transformers also reduces ongoing costs. Transformers are typically the most expensive asset in a substation, so any repairs or breakdowns are similarly pricey. Faster response times through online monitoring minimize these expenses.
When workers can find and fix issues faster, they’ll ensure the repair process is as easy as possible. Equipment costs and billing hours can both fall as a result. Preventing breakdowns will also cut expenses from lost productivity.
Proactive offline monitoring can also prevent these high costs, but manual checks are a more expensive process. Since offline solutions are more streamlined and don’t require downtime, they offer the same maintenance benefits with less lost time.
Longer Transformer Service Life
Another significant advantage of online monitoring is how it extends transformers’ lifespans. When employees can learn of and respond to issues faster, they’ll minimize any damage these systems experience. They’ll keep the equipment in optimal condition as a result and help it last longer overall.
Manual offline monitoring can also extend operating lifespans, but it’s harder to do so to the same extent. These methods are often too slow to find and resolve issues quickly — and performing them requires staffing levels and disruption many companies can’t afford.
Online monitoring solutions let workers maximize transformer life without these high requirements. Power companies can then ensure they get the highest ROI possible out of these expensive pieces of equipment.
Enabling Grid Modernization
Online monitoring for power transformers also has broader indirect advantages. Connecting transformers to online data-sharing platforms will give energy companies a better view of how the grid operates. This data enables more effective grid modernization initiatives in turn.
Transformer connectivity is a vital first step in many modernization efforts. One of the most crucial grid upgrades to make is implementing smart meters, which automatically adjust grid operations according to changing demand. To achieve that, grids need real-time insight into ongoing use, which online monitoring solutions provide.
Modernizing energy infrastructure will likely also bring about initial disruption. Real-time insight into any rising maintenance concerns is essential for managing these changes and online monitoring tools provide that. With these systems in place, energy providers can install upgrades without worrying about causing widespread issues.
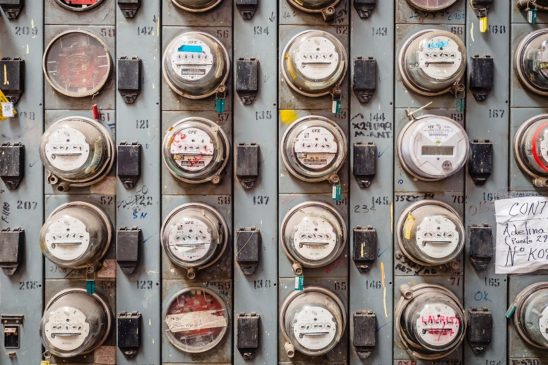
Ongoing Improvements
Similarly, online monitoring also gives companies insight into larger maintenance and performance trends. This information then lets power companies embrace a spirit of ongoing improvement, continuously optimizing their infrastructure for maximum performance and longevity.
Online systems can automatically create a digital, cloud-based record of maintenance history and performance readings. Energy companies can look across this data to see any recurring issues, highlighting a path toward overall improvement.
Optimizing any industrial system requires understanding where there’s room to improve. Digital paper trails and online monitoring solutions enable that knowledge. Energy infrastructure can then work past its most significant issues to reach its full potential.
Online Monitoring Is Critical for Power Transformers Today
Monitoring is a crucial part of transformer maintenance and online systems are the best way to perform this. These solutions ensure grids and substations get the most out of their power transformers.
Installing online monitoring systems will involve some disruption and costs. However, these benefits will make up for those expenses before long and enable future growth.
Emily Newton is the Editor-in-Chief of Revolutionized, an online magazine discussing the latest industry innovations and trends.
Oil and gas operations are commonly found in remote locations far from company headquarters. Now, it's possible to monitor pump operations, collate and analyze seismic data, and track employees around the world from almost anywhere. Whether employees are in the office or in the field, the internet and related applications enable a greater multidirectional flow of information – and control – than ever before.